Determining the best warehouse network size and footprint is a critical decision for any business to make. The right solution helps businesses achieve an efficient supply chain that delivers high levels of customer service, minimizes costs, and improves overall performance while paving the way for growth. However, by connecting warehouse networks to other supply chain resources and infrastructure, businesses can reach the next level of performance and competitiveness. Crafting the best connection strategy requires careful analysis by supply chain experts and a willingness to adapt.
Given the criticality of supply chains to the profitability of a business, leading enterprises continue to revise, revamp, and invest in warehouse build and placement strategies. The business press brims with stories that speak to a range of supply chain re-engineering efforts from some of the leading industry competitors in the race for market dominance:
- A large home improvement retailer is opening five “import distribution centers” that will serve as storage facilities for offseason goods until they are in demand, part of a $1.7 billion investment in a supply chain strategy the retailer says will help it more efficiently distribute its inventory across its more than 100 logistics facilities.
- A membership warehouse club announced it would open five new highly automated fulfillment centers this year, and about 14 to 16 warehouses in total over the next five years, as well as upgrade its existing network of 55 warehouses as it looks to build on e-commerce sales growth by speeding order fulfillment while cutting shipping costs.
- A national general merchandise retailer announced plans to open at least six more sortation centers across the U.S., adding to its network of nine centers as part of a $100 million investment. The new warehouses will let it fill more online orders, speed up delivery and cut down on shipping costs for its facilities that handled 26 million packages in 2022. The company expects to double package handling in 2023 by using its nearly 2,000 stores as distribution hubs.
Each one of these initiatives is a testament to the importance of maintaining a robust supply chain posture and a willingness to invest where the potential rewards are great.
The Omnichannel Connection
Among the common themes for advancing supply chains has been a growing trend of retailers packing e-commerce orders at their stores as well as at warehouses to speed deliveries and tap into more inventory. Companies can miss out on online sales if items are out of stock at the warehouse but in stock at a store. Adding the option to ship from a store allows retailers to avoid the “out of stock” message on websites that can send shoppers to rivals. Merchants also speed up delivery by taking advantage of the proximity their bricks-and-mortar sites have to customers relative to their warehouse locations.
The merits of connecting more of an enterprise’s physical assets to strengthen omni-channel capabilities are borne out by academic research as well. One study points out that, “by leveraging store and warehouse locations, and the inventory in stores and warehouses, omnichannel firms may achieve high levels of both customer service (by delivering online orders quickly and having products in stores) and economic performance (e.g., minimizing total cost or maximizing profit).” (Millstein et al., 2022). The same study emphasizes that even though their findings show that the “ship-from-warehouse” design generates greater profit than “ship-from store” strategies, the combination of “ship-from-store-and-warehouse” design is better than both of the standalone approaches, with the advantage growing as the percentage of online demand increases.
Companies can miss out on online sales if items are out of stock at the warehouse but in stock at a store. Adding the option to 'ship from a store' allows retailers to avoid the 'out of stock message on websites.
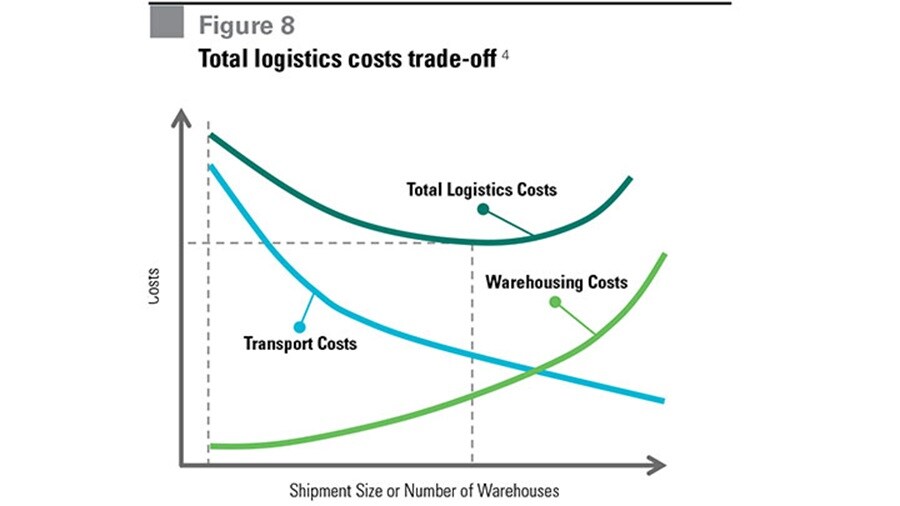
Warehouses – How Many and Where to Place Them?
Determining the number and placement of warehouse facilities requires a thorough exploration of numerous interconnected factors as outlined below. Common to all considerations, however, is the customer promise. It is essential to keep in mind the base promises made by the business that had set customer expectations to begin with, as well as the corresponding strategies required to meet those expectations. If “free shipping” was promised, then proximity to customers becomes particularly important to keep transportation costs in check. Just as important is whether customers expect delivery in 2-hours, 2-days, or 2-weeks. Each promise embodies requirements that directly impact the warehousing and distribution network. With the customer promise in mind, businesses will typically first determine the optimum number of facilities by type needed followed by placement considerations.
Key factors informing warehouse counts:
- Geographic reach: The spread of a company's customer base, suppliers, and manufacturing facilities will impact the ability make products available to customers quickly and efficiently. Key considerations include how the territory that can be serviced in two days. Is it possible to reach a target location overnight by air, or in two days by ground?
- Product variety and type: Different products may have different storage and transportation requirements thereby making discrete facilities preferred. Examples include high value items vs. low, high velocity items vs. low turnover, perishable vs. non-perishable.
- Transportation costs: If transportation costs are high, it may be more cost-effective to have additional warehouses located closer to customers (up to the point of diminishing returns).
- Inventory costs: Having too many warehouses can increase inventory costs, while having too few can result in stockouts and lost sales.
- Manufacturing Environment: Operational requirements may dictate which products and/or services can be supported at any given facility, whether an enterprise utilizes make-to-stock, make-to-order, assemble-to-order, engineer-to-order or other approach.
- Supply and Demand Variability: The greater the variation in a supply chain, the higher the safety stock inventory requirements. This can translate into a greater need for warehouse space, either in the form of more locations or larger facilities. Such a scenario played out during the pandemic when consumer demand spike coupled with ocean service disruptions led many companies to over order while scrambling for temporary storage.
Placement is the second order of business, though tightly tied to the ideal number of facilities. Placement is the determination of the best location for each warehouse or distribution point in consideration of cost efficient access to supply, markets, and transportation.
Key factors informing warehouse placement:
- Proximity to customers: By locating the warehouse closer to the customer, transportation costs and lead times can be reduced, resulting in delivery times that meet customer promise standards. The closer the warehouse can be to the largest 15-20 largest population centers in North America, the better.
- Transportation infrastructure: The availability and quality of highways, railroads, and airports greatly impact the efficiency and cost-effectiveness of warehouse operations. This fact is not lost on terminal operators who continue invest in strategic places like Mobile, Ala., where APM Terminals announced a $60M rail expansion to double capacity.
- Labor availability: A location with a high availability of skilled workers can result in increased productivity and reduced labor costs,
- Real estate costs and availability: Costs can vary greatly depending on location and have a direct impact on overall profitability. Real estate near key ports remains scarce, with availability rates near Los Angeles and New York/New Jersey ports under two percent.
- Taxes and regulations: The tax environment and regulations can impact costs significantly.
- Risk and security: Locations prone to natural disasters, security threats or other risks may increase the costs and risks associated with warehouse operations.
Optimizing Supply Chain Facility Numbers and Placements
Ultimately, the optimal number and placement(s) for a supply chain infrastructure will depend on the unique characteristics of the company's supply chain and the specific objectives of the operation. Several implementation strategies include, but are not limited to:
- Consolidation: Consolidating multiple smaller warehouses into fewer, larger ones can help to reduce operating costs and improve efficiency.
- Co-location: Co-locating warehouses with other facilities, such as manufacturing plants, can help to reduce transportation costs and improve coordination between different supply chain functions.
- Cross-docking and Transload: These activities have the potential to reduce inventory holding costs and improve delivery times as well as possibly eliminating the need for warehouse storage altogether. They also provide the opportunity for postponement on final routing and for segregating goods shipped internationally at country of destination rather than at the country of origin. This facilitates better insight on how best to direct goods to meet current market demand and can achieve significant savings, especially for retailers.
- Timing: Having clarity around the timing of business cycles relative to the time it would take to secure and launch new supply chain infrastructure will inform when a move may be feasible. From the time business strategy commitments are made, launching a new site can range from 2-3 months for an existing facility to 9-months or longer when advanced automation is involved.
The Right Supply Chain Partner
Once an optimization plan is in hand, finding the right partners with the information and resources to execute is key. Implementing even one of the optimization strategies can significantly help fine tune a warehouse network while reducing costs and improving overall supply chain efficiency and performance.
For each decision along the way, one should leverage the data-driven insights that identify the options best suited to the strategy. Data can inform every aspect, whether it is local labor and real estate costs, production, or transportation timelines. Using network optimization software can help model different warehouse scenarios and determine the optimal number and location of warehouses based on various factors. Some inputs – like what off-market real estate may soon become available to meet your needs – require intelligence known only to the smallest of circles.
Finally, choose a partner with a track record of dependability and connections. There are tangible benefits to working with collaborators that bring financial stability and strong credit lines to the negotiation table on your behalf, making an attractive candidate in the competition for limited space. Last, with access to capacity across air, land, and ocean, a connected supply chain can elevate your enterprise to the next level of performance and growth.
The content herein is comprised of general considerations. The Maersk organization includes subsidiary companies that provide warehousing and logistics services worldwide. For additional information or to discuss strategies for strengthening the connections and productivity in your specific supply chain, visit Maersk.com or contact your local Maersk representative.
1Millstein MA, Bilir C, Campbell JF. The effect of optimizing warehouse locations on omnichannel designs. Eur J Oper Res. (2022) 301:576–90. doi: 10.1016/j.ejor.2021.10.061
2Prologis Research based on Herriot-Watt University, https://www.prologis.com/logistics-industry-research/europes-most-desirable-logistics-locations-1
Connect with our experts
Thank you
Something went wrong
Connect with our experts
To learn more about our warehousing and distribution services to optimize your network.
Anything you need, we’re here to help
By submitting this form, I agree to receive logistics related news and marketing updates from A. P. Moller-Maersk and its affiliated companies via e-mail. I understand that I can opt out of such Maersk communications at any time. To see how we process your personal data, please see our Privacy Notification.